Understanding the Advantages of Using Profile in PVC for Your Business
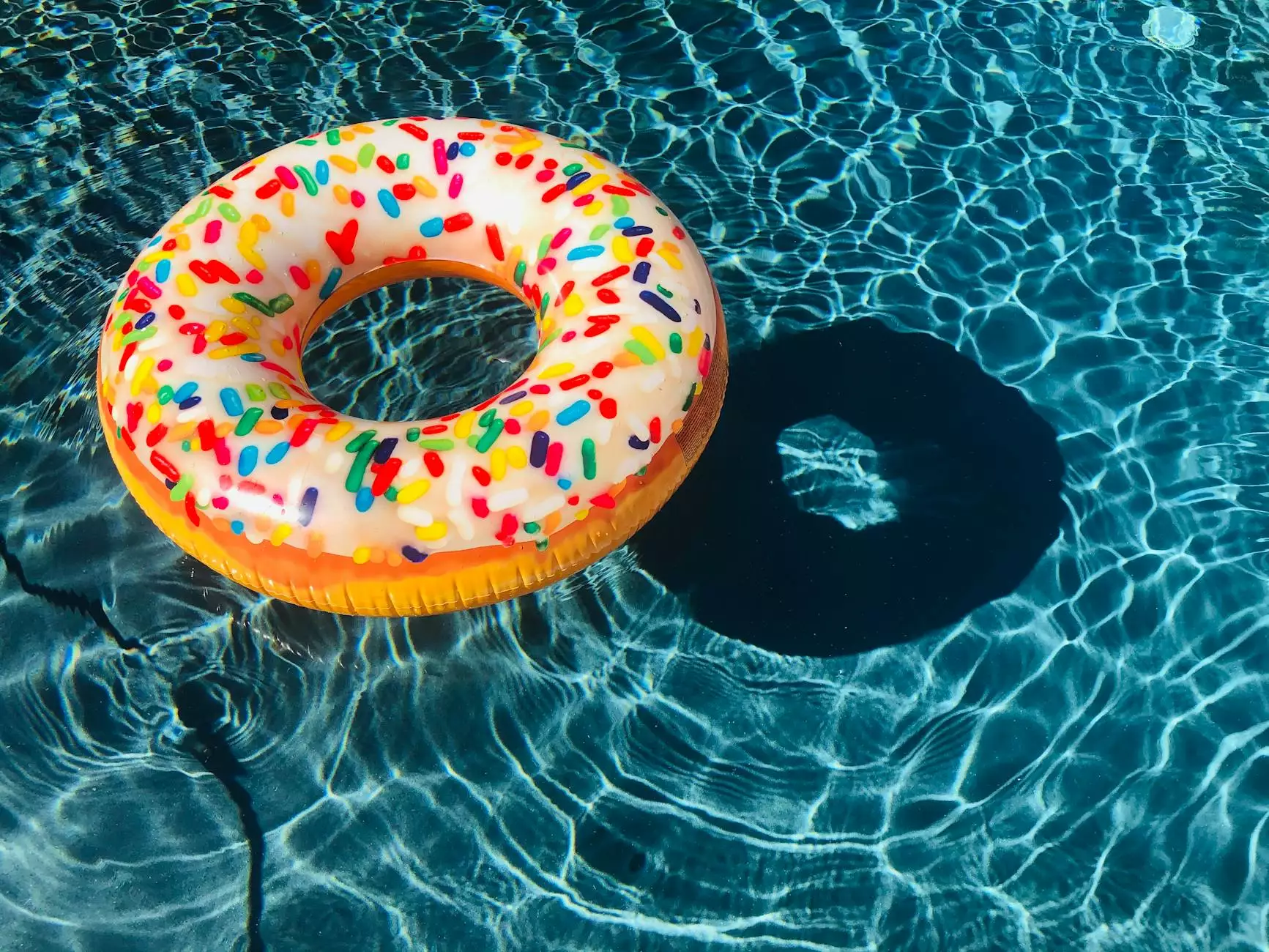
In today’s competitive business landscape, selecting the right materials for your projects can significantly impact overall cost, efficiency, and finished product quality. One material that has gained immense popularity across various industries is profile in PVC. With numerous applications ranging from construction to automotive, PVC (Polyvinyl Chloride) stands out due to its unique properties and advantages.
What is PVC?
PVC, or polyvinyl chloride, is a synthetic plastic polymer widely used in a variety of products and applications. Known for its durability, versatility, and cost-effectiveness, PVC is one of the most produced synthetic plastic polymers globally. Depending on the formulation used, PVC can create both rigid and flexible products, making it suitable for a wide range of applications.
Understanding Profile in PVC
A profile in PVC refers specifically to PVC that has been shaped through extrusion to create a linear continuous shape. This can take the form of pipes, sheets, or various shapes designed for specific functions. The extrusion process involves melting PVC resin and forcing it through a shaped die to create the desired profile.
Applications of Profile in PVC
The versatility of profile in PVC means it can be applied across different sectors. Here are some key applications:
- Construction: PVC profiles are commonly used in window frames, doors, and cladding. They offer excellent thermal insulation and noise reduction.
- Automotive: In the automotive industry, PVC profiles are used for weather stripping, interior panels, and insulation materials.
- Electrical: Flexible PVC profiles are widely used in producing electrical insulation and cable sheathing.
- Furniture: PVC profiles are also increasingly used in furniture design, providing a lightweight yet durable alternative to traditional wood products.
Benefits of Profile in PVC
1. Durability and Longevity
One of the primary advantages of using profile in PVC is its remarkable durability. PVC is resistant to environmental factors such as moisture, rot, and corrosion, which makes it an ideal choice for both indoor and outdoor applications. For example, in construction, PVC window frames can last for decades with minimal maintenance, unlike wood that requires treatment to prevent decay.
2. Cost-Effectiveness
Another significant benefit is the cost-effectiveness of profile in PVC. When compared to other materials like wood and metal, PVC is often less expensive to produce and install. This is particularly advantageous for large-scale projects where material costs can accumulate rapidly. Additionally, its low maintenance requirements further contribute to overall cost savings over time.
3. Design Flexibility
Profile in PVC offers exceptional design flexibility. The extrusion process allows for custom shapes and sizes, accommodating the specific requirements of various projects. Businesses can easily achieve unique designs without the limitations often associated with traditional materials.
4. Environmental Impact
While the environmental impact of plastic products is often scrutinized, it’s essential to note that PVC is recyclable. Companies can utilize recycled PVC to produce new profiles in PVC, reducing waste and promoting a more sustainable approach to production and consumption. This recycling process aligns with the growing corporate responsibility towards sustainable practices.
5. Safety and Non-toxicity
Modern profile in PVC products are developed to be safe and non-toxic. By following stringent regulations, manufacturers ensure that the PVC used is free from harmful substances. This makes it suitable for a wide range of applications, including those involving direct contact with consumers.
The Manufacturing Process of Profile in PVC
The manufacturing process of profile in PVC involves several critical steps that ensure its quality and effectiveness:
- Material Selection: Choosing the right PVC resin based on the required properties for the finished product.
- Mixing: Combining PVC resin with additives such as plasticizers, stabilizers, and colorants to enhance performance.
- Extrusion: Melting the PVC mixture and forcing it through a die to shape it into the desired profile.
- Curing: Allowing the material to cool and harden, ensuring it retains its shape and structural integrity.
- Finishing: Trimming, cutting, and surface treating the profiles to meet specific client requirements.