The Comprehensive Guide to PC ABS in 3D Printing
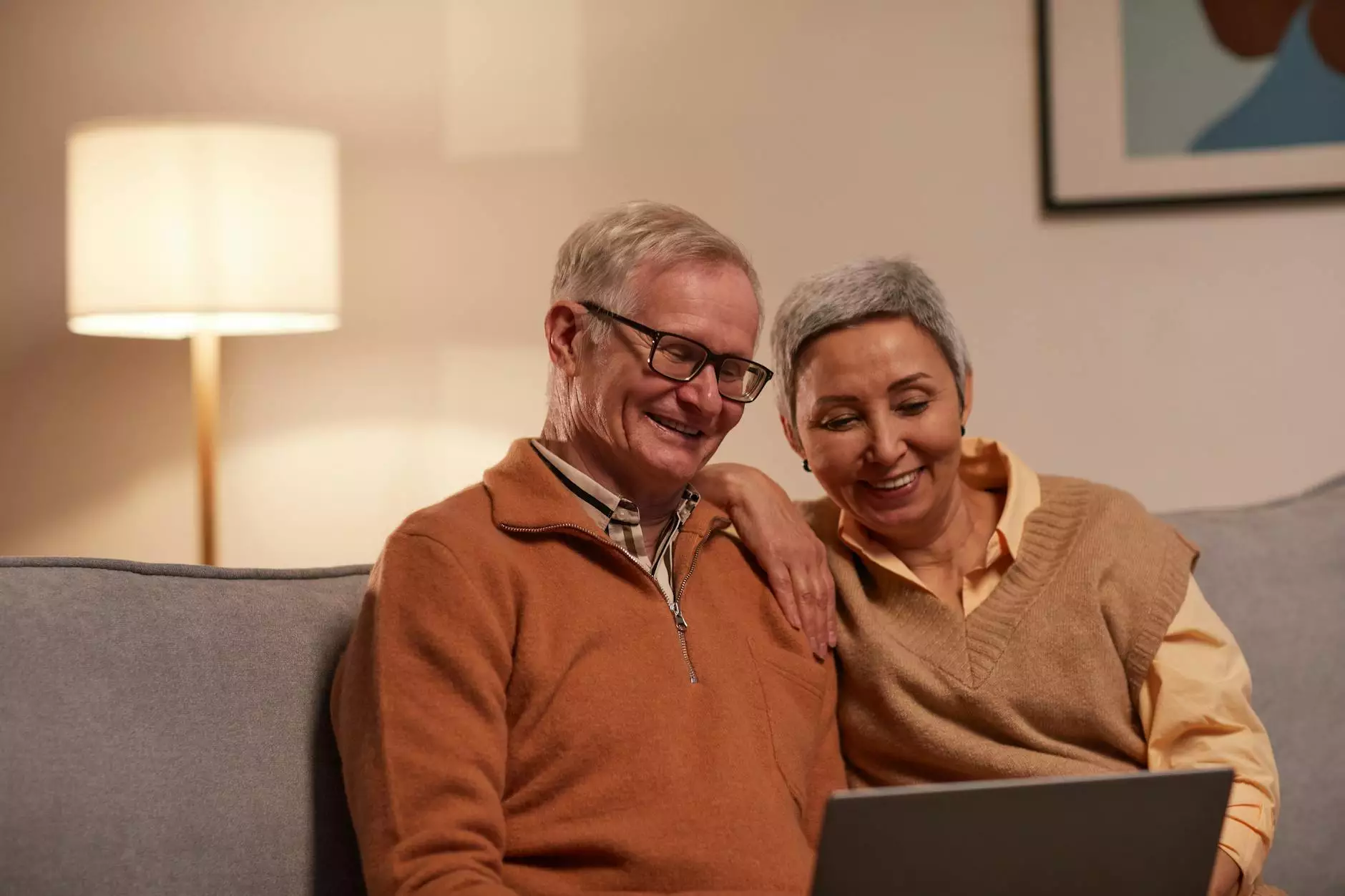
PC ABS, a blend of Polycarbonate (PC) and Acrylonitrile Butadiene Styrene (ABS), has emerged as a remarkable material in the world of 3D printing. This article delves into the multifaceted applications of PC ABS in the 3D printing industry, outlining its characteristics, advantages, and how it outperforms other materials.
Understanding PC ABS
PC ABS is a thermoplastic that combines the strength and heat resistance of Polycarbonate with the easy processability of ABS. This combination results in a material that effectively addresses the challenges faced in both functional and aesthetic parts during the 3D printing process.
1. The Science Behind PC ABS
To truly appreciate the benefits of PC ABS, it's essential to understand its composition. The polycarbonate component lends strength and toughness, while the ABS component ensures that the material is easy to mold and shape. This unique synergy enables 3D printers to produce parts that are not only robust but also lightweight.
2. Key Properties of PC ABS
- Impact Resistance: PC ABS is known for its high impact resistance, making it an ideal choice for parts subjected to stress and force.
- Heat Resistance: It can withstand higher temperatures than standard ABS, allowing for more versatile applications.
- Surface Finish: The surface of PC ABS prints can be smooth or textured, accommodating a range of design needs.
- Dimensional Stability: PC ABS maintains its form better during and after the printing process, reducing warping and improving accuracy.
- Ease of Printing: Designed for ease of use, PC ABS is compatible with various 3D printing technologies, including FDM (Fused Deposition Modeling).
The Benefits of Using PC ABS for 3D Printing
When considering materials for 3D printing, PC ABS stands out for several compelling reasons:
1. Versatility in Applications
PC ABS is suitable for a wide range of applications, from industrial parts to prototypes. Its blend of strength and flexibility caters to diverse industries including automotive, aerospace, and consumer goods. This versatility allows designers and engineers to push the boundaries of what’s possible in their projects.
2. Cost-Effectiveness
Despite its high-performance characteristics, PC ABS remains an economical choice compared to pure polycarbonate, making it accessible for companies looking to maximize their ROI. This financial aspect often makes it a go-to material for both production and prototyping processes.
3. Enhanced Aesthetic Appeal
For projects requiring a polished finish, PC ABS provides excellent surface quality that can be further enhanced through post-processing techniques. This allows products not only to function well but also to look appealing to end-users, an essential factor in competitive markets.
Optimal Printing Techniques for PC ABS
To achieve the best results when printing with PC ABS, several techniques and considerations should be kept in mind:
1. Printer Compatibility
Ensure that your 3D printer is compatible with high-temperature materials. A printer with an all-metal hotend is often required for optimal performance with PC ABS.
2. Print Bed Adhesion
Utilizing a heated print bed can enhance adhesion and reduce warping. It’s recommended to maintain a print bed temperature between 80°C and 110°C.
3. Print Settings
Adjusting print speed, layer height, and nozzle temperature is crucial for achieving the best quality results. For PC ABS, a nozzle temperature of 250°C to 280°C is generally recommended.
Post-Processing Techniques for Enhanced Results
After printing, PC ABS parts can undergo various post-processing techniques to improve their finish and functionality. Here are some popular methods:
- Sanding: For achieving a smooth surface, sanding the printed parts can be very effective.
- Painting: PC ABS can be painted easily, allowing customization and brand alignment for product aesthetics.
- Vapor Smoothing: Using acetone vapor can enhance the finish of ABS components, creating a glossy surface.
Environmental Considerations
As businesses increasingly prioritize sustainability, it’s important to note that PC ABS has recyclable properties. Companies like infotron.com.tr are exploring ways to incorporate sustainable practices in their 3D printing processes, making material reuse and recycling a feasible option.
The Future of 3D Printing with PC ABS
The evolution of PC ABS in 3D printing is promising. As technology advances, we can expect enhancements in printing techniques and material formulations that will further leverage the advantages of PC ABS. Innovations could lead to improved durability, reduced costs, and expanded application opportunities.
1. Integration with New Technologies
Emerging technologies, like AI-driven design software and advanced printing techniques such as multi-material printing, will likely take PC ABS applications to the next level. This could revolutionize industries by allowing for complex designs that are both functional and cost-effective.
2. Industry Adoption
With companies increasingly adopting 3D printing for production-level applications, the demand for materials like PC ABS will continue to grow. Businesses that stay ahead of this trend by integrating PC ABS into their workflows will find themselves better positioned in their respective markets.
Conclusion
In conclusion, PC ABS stands out as a premier material in the 3D printing landscape, thanks to its unique blend of strength, versatility, and aesthetic flexibility. As industries evolve and demand for innovative products increases, PC ABS will play a critical role in meeting these challenges. Companies such as Infotron are well-poised to make the most of this remarkable material, pushing the boundaries of design and manufacturing in the process.
By understanding the properties, benefits, and optimal practices related to PC ABS, businesses can effectively enhance their 3D printing capabilities and overall production quality, making a significant impact on their success in the ever-evolving market.