The Ultimate Guide to Die Casting Supplies for Metal Fabricators
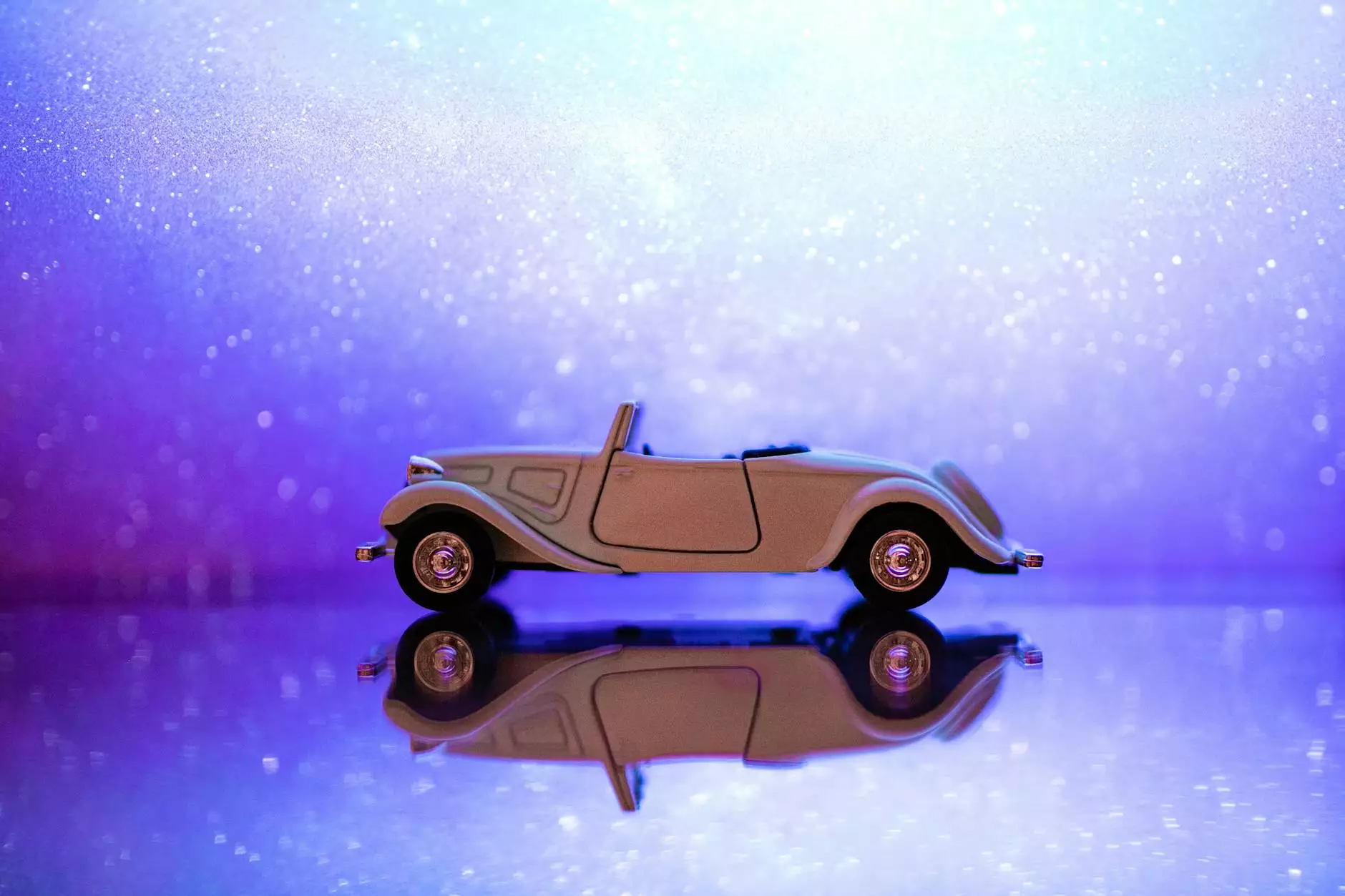
In the fast-paced world of metal fabrication, the importance of using high-quality die casting supplies cannot be overstated. Whether you are a seasoned professional or just starting your journey in the industry, understanding the significance of the materials and processes involved can make a profound difference in the quality of your final products. This comprehensive guide will delve into the essential die casting supplies, their applications, benefits, and how they can optimize your manufacturing process.
What is Die Casting?
Die casting is a metal casting process that uses liquid metal, which is forced into a mold cavity under high pressure. This method is highly valued for its ability to produce detailed and complex parts with a high level of precision. The die casting process is widely used in various industries, including automotive, aerospace, and electronics, making it a crucial aspect of metal fabrication.
Key Die Casting Supplies Required for Metal Fabricators
To achieve optimal results in die casting, here are some of the essential supplies you will need:
1. Die Casting Machines
At the heart of the die casting process is the die casting machine. This machine applies pressure to inject molten metal into the die. There are various types of die casting machines, including:
- Hot Chamber Machines: Best for alloys with low melting points, such as zinc or magnesium.
- Cold Chamber Machines: Suitable for metals with higher melting points like aluminum and copper.
2. Die Sets
The die sets are the molds used to shape the molten metal. They can be quite complex and vary in design based on the part being manufactured. Quality die sets ensure accurate and consistent production. It’s crucial to select die sets made from durable materials that can withstand the stresses of repeated use.
3. Alloys and Metal Materials
The choice of alloys significantly affects the properties of die-cast products. Common alloys used in die casting include:
- Zinc Alloys: Known for their excellent fluidity and dimensional stability.
- Aluminum Alloys: Highly versatile with good corrosion resistance and strength-to-weight ratio.
- Magnesium Alloys: Lightweight and have superior toughness, making them ideal for automotive applications.
4. Lubricants
Lubricants are essential in the die casting process to reduce friction between the molten metal and the die surfaces. This helps in achieving a smooth finish on the cast products while also prolonging the life of the die. Common types of lubricants include:
- Die Lubricants: Applied to the die surface.
- Release Agents: Facilitate the easy removal of the cast part from the die.
5. Cooling Systems
Effective cooling systems are vital for maintaining the temperature of the die during production, which ensures uniform solidification and reduces defects. Cooling can be managed through:
- Water cooling: Circulating water through channels in the die.
- Air cooling: Using air to dissipate heat quickly.
6. Inspection and Quality Control Tools
After production, ensuring the quality of the die-cast parts is crucial. Inspection tools like precision measuring instruments and non-destructive testing methods help verify if the parts meet the required specifications. Common tools include:
- Calipers: For measuring dimensions.
- Surface Roughness Testers: To assess the surface quality.
- X-ray Inspection Systems: For detecting internal defects.
Benefits of High-Quality Die Casting Supplies
Investing in quality die casting supplies brings multiple benefits:
1. Enhanced Production Efficiency
High-quality materials and tools can significantly enhance production efficiency, reducing cycle times and waste.
2. Improved Product Quality
Using superior die casting supplies guarantees a higher quality of finished products with better surface finishes and dimensional accuracy.
3. Cost-Effectiveness
Although quality supplies may require a higher initial investment, they lead to fewer defects, less downtime, and lower maintenance costs over time, making them a cost-effective choice in the long run.
4. Flexibility in Design
With advanced die casting supplies, manufacturers can push the boundaries of design, producing more complex and innovative parts that meet the evolving needs of various industries.
Choosing the Right Die Casting Supplies for Your Business
Selecting the most suitable die casting supplies for your metal fabrication business requires careful consideration:
1. Assess Your Production Needs
Understand the specific requirements of your projects, including the type of metals, the complexity of designs, and the expected production volume.
2. Research Suppliers
Investigate potential suppliers to assess their reputation, product offerings, and customer service. Companies like DeepMould.net provide a wide range of high-quality die casting supplies tailored for diverse fabrication needs.
3. Evaluate Quality Certifications
Choose suppliers whose products meet industry-quality standards and certifications. This guarantees that you are investing in reliable and durable materials.
The Future of Die Casting Supplies
The die casting industry is evolving rapidly, with innovations continually enhancing the quality and efficiency of die casting processes. Here are some trends to watch:
1. Automation and Smart Manufacturing
As automation becomes integral to manufacturing, businesses that leverage advanced robotics and AI for die casting are likely to see substantial efficiency gains.
2. Sustainable Practices
With an increasing focus on sustainability, the demand for eco-friendly die casting supplies, including recyclable materials and energy-efficient processes, is on the rise.
3. Customization Options
The ability to customize die casting materials and processes will continue to grow, allowing businesses to produce tailored parts that meet specific client requirements.
Conclusion
In the competitive field of metal fabrication, the quality of your die casting supplies can set you apart from the competition. By investing in high-quality materials and processes, you position your business to produce superior products that meet the evolving demands of your customers. For those looking to thrive in the die casting landscape, establishing a reliable supply chain with reputable providers like DeepMould.net is essential. Equip your business with the best die casting supplies and watch your production efficiency and product quality soar.
Stay informed and adaptable to innovation in materials and technology, ensuring that your business remains at the forefront of the die casting industry.